Firmengeschichte
Der Anfang der FRAnkenberger MOtorenwerke
Im April 1923 gründeten Dr.-Ing. h. c. J. S. Rasmussen und die Ingenieure Blau und Figura die Metallwerke Frankenberg/Sa. GmbH. Dieser Betrieb arbeitete anfangs nur für das Zschopauer Motorradwerk. Sättel, Kupplungen, Vergaser, Gepäckkoffer und andere Motorradteile für DKW standen auf der Produktpalette.
Die hohe Qualität der Erzeugnisse, Fleiß und Zuverlässigkeit der Arbeiter und ein niedriger Preis führten schnell zum Interesse auch anderer Motorradhersteller, und so konnte die Belegschaft von ursprünglich 30 Arbeitern bereits 1929 auf 700 Beschäftigte erhöht werden.
In dieser Zeit wurde vielerorts an der Entwicklung der Automobile, besonders für den Personentransport gearbeitet, die Interessen der privilegierten Gesellschaft standen voran. Bei DKW wurden Versuche am Kleinwagen durchgeführt. Mit dem Geschick der bewährten Facharbeiter sollte ein Personenkraftwagen der untersten Klasse entstehen – einfach, billig und doch leistungsfähig.
Auch die Motorradproduzenten suchten nach Lösungen für höhere Marktanteile. Und so lag es nahe, daß in dieser Zeit die technische Einfachheit des Motorrades mit den breiteren Einsatzmöglichkeiten des Autos gepaart wurde. Die Dreiräder entstanden in vielen Varianten. In Frankenberg begann man die Entwicklung 1927.
Der Stammvater der Framo- und späteren Barkas-Transporter wurde als „DKW-Eilliefer-wagen“ entwickelt und als TV 300 1927 auf den Markt gebracht. Für Handwerker und ambulante Händler fand das vielseitig einsetzbare Dreirad (mit Frontantrieb) großes Interesse.
Die beiden Grundtypen
- Pritschenaufbau (offene Ladefläche)
- Kastenaufbau (geschlossener Laderaum)
sind noch heute die Basis für viele nach dem Einsatzzweck entwickelte Ausführungen.
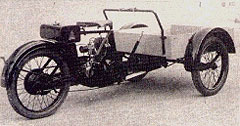
Prototyp von 1926
Der Grundgedanke, mit dem minimalen Aufwand viel zu transportieren, führte schon 1926 zu Prototypen, man kann sagen zum Motorrad-Transporter.
Das Dreiradfahrzeug wurde von einem luftgekühlten Einzylinder-DKW-Motor mit
300 cm³ (7 PS) betrieben. Die Motoren lieferten die Zschopauer Motorenwerke, dort profitierte Rasmussen auch als DKW-Gesellschafter. Der Antrieb über eine Kette auf das Vorderrad bewegte das mit max. 500 kg beladene Fahrzeug (einschließlich Fahrer) bis zu einer Geschwindigkeit von 40 km/h.
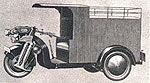
Transportdreirad TV 300
Die Charakteristik dieser Fahrzeugkategorie, mit minimalstem Aufwand Güter und später auch Personen zu transportieren, also schlechthin „Transporter“ zu sein, drückte sich in dieser Zeit noch in der Bauweise aus:
Obwohl die Windschutzscheibe für die PKW schon erfunden war, gab es für den Fahrer keinen Schutz, Motorabdeckung und Kettenschutz fehlten. Mit dem einfachen Trapezlenker wurde ein Wendekreisdurchmesser von 6,5 m erreicht. Es gab keinen Anlasser und keinen Rückwärtsgang.
Das Mischungsverhältnis für die Zweitaktmotoren lag damals noch bei 10:1.
Zur schnellen Einführung trug sicher das Verkaufsargument „Ist mit Führerschein für Motorräder zu fahren“ wesentlich bei, ebenso die leichte Zugänglichkeit bei Reparatur- und Wartungsarbeiten. Geschmiert wurde noch an vielen Stellen und oft, zumal dazu keine besonderen technischen Kenntnisse nötig waren.
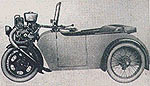
Prototyp ZW 200
Dass sich Rasmussen noch nicht ausschließlich auf den Transporterbau festgelegt hatte, beweist der Prototyp ZW 200. Dieses Dreirad für den Sonntagsausflug der sog. Bemittelten blieb bis Ende 1930 in der Produktion und wurde dann von einem Leichttransportrad LT 200 mit 200 cm³ oder 300 cm³ abgelöst.
Der luftgekühlte Einzylindermotor mit 192 cm³ Hubraum leistete 6 PS, mit 295 cm³ Hubraum wurden 7 PS erreicht.
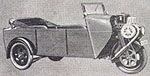
Transportdreirad LT 200
Für die Festlegung des Hubvolumens war maßgebend, dass jedes angefangene Hundert die Kraftfahrzeugsteuergruppe bestimmte und Fahrzeuge mit Motoren bis 200 cm³
führerscheinfrei gefahren werden konnten. Wie zündend die Idee mit dem billigen Dreirad war, zeigte der Export des Antriebsaggregats mit Zentralrohrrahmen und Sonderaufbau nach Indien. Mit den Nutzfahrzeugen konnte sich das Frankenberger Werk eine Vormachtstellung auf dem Markt erarbeiten, während die reinen Personenkraftwagenhersteller Absatzprobleme hatten.
Ingenieure und Arbeiter entwickelten neue Modelle und sicherten damit auch ihre Arbeitsplätze. Der Typ LTH 200 und 300 entstand. Aus dem Transportdreirad wurde mit Motorhaube, Fahrerhaus und Lenkrad-Schneckenlenkung ein „echtes“ Automobil. Der wirtschaftliche Aufschwung um 1930 brachte auch viele Transportprobleme. Die im Kutsch- und Pferdewagenbau erfahrenen Wagenbauer fühlten sich herausgefordert und entwickelten die ersten spezifischen Aufbauten, so z.B. die Firma Steinberg in Recklinghausen.
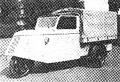
LTH
Selbst als Sattelschlepper, natürlich mit den Grenzen, die geringe Motorleistung und Fahrmechanik setzen, bewährte sich das Dreirad.
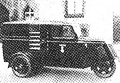
LTH-Dreiräder
Die günstigen Absatzmöglichkeiten, die Steigerung der Produktion und das Anwachsen der Belegschaft, führten immer wieder zu Erweiterungen, bis schließlich die ehem. Trainkaserne in Frankenberg nicht mehr ausreichte, wieder „anders“ genutzt werden sollte und der Betrieb 1933 etappenweise in das benachbarte Hainichen übersiedelte.
Die in Konkurs geratene Woll-Haar-Kämmerei und Spinnerei des Nordwolle-Konzerns war als neue Produktionsstätte ebenso günstig wie die Arbeitskräfteanlage in dieser traditionsreichen Weberstadt.
Am 1.1. 1934 erfolgte die Umbenennung des Betriebes in Framo-Werke GmbH Hainichen (Frankenberger Motorenwerke).
Anfang der 30er Jahre wurden die Erkenntnisse des Leichtbaus auch auf Personenkraftwagen übertragen, so entstanden die Typen Framo-Stromer und Framo-Piccolo.
- Framo-Stromer
- Framo-Piccolo
Diese beiden Personenkraftwagen hatten jedoch wenig Chancen, bedeutende Marktanteile zu gewinnen, weil schon eine Reihe Kleinwagen angeboten wurde. Bereits 1924 fertigte Opel den „Laubfrosch“ (natürlich in Grün), BMW den „Dixi DA 1“ (1928 in Eisenach) und Hanomag das „Kommißbrot“ (1925).
Aber auch mit dem „Stromer“ und dem „Piccolo“ wurde ein Stück Fahrzeuggeschichte, besonders im Leichtbau und zur Abklärung prinzipieller technischer Tendenzen und ökonomischer Gesichtspunkte, geschrieben.
Fragen, wie Front- oder Heckantrieb; Stahl, Gummi- oder Luftfeder; Holz- oder Blechkarosserie; Dreirad- oder Vierradwagen wurden zur Diskussion gestellt. Noch heute achten wir das Können und den Fleiß der Arbeiter und Ingenieure, die mit Mut zum technischen Fortschritt und durch Präzisionsarbeit die unteren Grenzen des Aufwandes für den Bau von Personenkraftwagen und Transportern bei möglichst hohem Effekt für den Nutzer gesetzt haben.
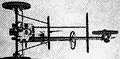
Framo FP 200
Die speziellen Erfahrungen mit den rentablen Dreirädern für die täglichen kommunalen Aufgaben und der stabile Absatz waren maßgebend für die Fortsetzung der Transportertradition. Den Anforderungen der Kunden und den Profitinteressen der Firmenleitung wurde mit der Entwicklung neuer, für die Einsatzfälle spezialisierter Fahrzeuge entsprochen, und damit wurden begehrte Handelsobjekte bereitgestellt, die in vielen europäischen Ländern, in Südamerika, der Sowjetunion und in Indien zum Einsatz kamen.

Montagebänder
In systematischer Weiterentwicklung entstanden die Dreiräder LTP 200 und 300 mit einer Tragfähigkeit von 600 kg und Pendelferderung.
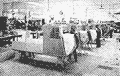
Montagebänder
Der LTG 200, Typ „Leipzig“, hatte ein vom Motor getrenntes Getriebe mit Einzylinder-DKW-Motor, 200 cm³, luftgekühlt, drei Vorwärtsgängen und einem Rückwärtsgang. Die Karosserie in Gemischtbauweise bestand aus einem mit Blech beschlagenem Holzgerippe. Das Fahrzeug erreichte voll beladen eine Höchstgeschwindigkeit von 40 km/h.
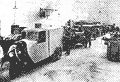
Montagebänder
Der LTG 500, Typ „Hamburg“, war bereits mit einem Zweizylinder-DKW-Motor mit 500 cm³ Hubraum ausgerüstet. Mit einer Motorleistung von 15 PS erreichte der LTG 500 bei 750 kg Nutzlast bereits die beachtliche Höchstgeschwindigkeit von 70 km/h.
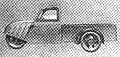
LTG 200 bzw. 500
Die schlimmsten Jahre
1934 wurde der erste Framo-Transporter mit vier Rädern gebaut und damit das Typprogramm für den Transporterbau bis zum Jahr 1943 festgelegt. Zu diesem Programm gehörten die Vierradwagen: FPT 300, HT 600, HT 1200, V 1200, LTV 500, V 500, V 501/1, V 500/2 und die Dreiradwagen: LTP 200, LTP 300, LTG 500, LTG 200. Ab 1937 wurden bei den Dreirädern 2-Zylinder-Zweitaktmotoren von DKW eingesetzt. Bei den Vierrädern kamen für die Typen HT 1200 und V 1200 4-Zylinder-Viertaktmotoren zum Einsatz.
Die Vierradtransporter wurden mit Hinterradantrieb produziert. Offensichtlich waren die Erkenntnisse der Kraftfahrmechanik, die daraus abgeleiteten Bedingungen für die Achslastverteilung und die deshalb auch negativen Erfahrungen mit frontgetriebenen Personenkraftwagen der Grund für diese Entscheidung.
In einer durchschnittlichen Produktion von 3000 Wagen jährlich wurden an zeitweise bis zu 6 Montagelinien unterschiedliche Fertigungstechniken serienmäßig eingesetzt, wie selbsttragende Sperrholzkarosserie für den Kastenwagen (FPT 300) oder Pritschenwagen mit Fahrgestell.
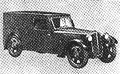
FPT 300
Staatsmonopolistische Interessen und die bereits 1938 auf Hochtouren laufende faschistische Rüstungsindustrie wirkten sich in allen Wirtschaftszweigen aus, drängten die Bedürfnisse der Bevölkerung vor allem Handwerker und Kleingewerbebetreibenden zurück und profilierten auch die Fahrzeugproduktion für die Aufrüstung. Ein sogenanntes Schnell-Programm beinhaltete Festlegungen für die Typen in der Kraftfahrzeugindustrie. Danach sollten nur noch die Dreiradfahrzeuge „Tempo“ und „Goliath“ gebaut werden. Nach der Einstellung der Dreiradproduktion 1938 wurde der festgelegte Einheitstyp V 501 auf der Basis des V 500 von 1939 bis Herbst 1943 produziert. Mit dem Einsatz des sog. U-Motors (U-500) kam der erste Framo-Motor 1943 in den V 501/2 (siehe Typentafeln 1927-1943).
Die inzwischen auf 100 Beschäftigte angestiegene Belegschaft fertigte zur zeit des Ausbruches des schrecklichen zweiten Weltkrieges 5750 Fahr-zeuge/Jahr, u.a. für den Export in die Balkanstaaten, sowie in die Länder Sowjetunion, Indien, Schweiz, in die skandinavischen Länder und nach Südamerika.
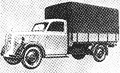
Framo HT 1200
Der weiterentwickelte V 501/2 wurde nach Unterlagen von Framo in kleinen Stückzahlen auch bei Standard, Manderbach und Ostner gebaut. Die wegen ihrer Zweckmäßigkeit vielseitig bewährten Fahrzeuge mit zivilem Abstrich und Framo-Zeichen waren bereits auf ihre Eignung für den militärischen Einsatz getestet und in den Geheimplänen für den räuberischen Überfall auf friedliche Länder verankert. der „Betriebsführer“ Rasmussen formierte seine „Gefolgschaft“ in Sinne des Weltherrschaftsdenkens z.B. in einem schriftlichen Aufruf so, dass es an der Zeit sei, den Grundstein für das Europa zu legen, in dem sich Deutschland den Platz“ an der Sonne“ sichert. Neben der Fahrzeugproduktion wurde mit steigenden Dividenden für die Gesellschafter Kriegstechnik, wie Panzerabwehrkanonen, Nebelwerfer, Bordwaffen, Richtmaschinen u. a., hergestellt, die ab 1.10.1943 solche Auftragshöhe erreichte, dass keine Fahrzeuge mehr produziert werden konnten und durften.
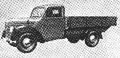
Framo-Lieferwagen
Mit Kriegsgefangenen, ausländischen Zwangsarbeitern und politischen Häftlingen stieg der Profit an der Kriegsproduktion. Zum Beispiel erhielt der Kaufmännische Direktor 1942 ein um 93% höhere Dividende als 1940. Der Bevölkerung wurden bei ständig wachsenden Entbehrungen zunehmend höhere Leistungen am Arbeitsplatz abgefordert.
Der Neubeginn
In den Maitagen des Jahres 1945 wurden die Antifaschisten von der Roten Armee aus Konzentrationslagern und Gefängnis befreit, die Reste des faschistischen Widerstandes zerschlagen, die ersten Befehle des Obersten Chefs der Sowjetischen Militäradministration erlassen und damit der demokratische Neubeginn eingeleitet.
Die in Hainichen eingerückten Truppen der Sowjetarmee organisierten die städtischen Organe der Selbstverwaltung, setzten sich mit dem überlassenen Chaos auseinander und weckten mit Kommunisten – den Aktivisten der ersten Stunde – den Willen zur Aufbauarbeit.
Zunächst fanden sich 50 vom Aufbauwillen beseelte Männer und Frauen, Konstrukteure und erfahrene Arbeiter zusammen, um die Geschicke des Betriebes in ihre Hände zu nehmen. Bald wuchs ihre Zahl auf 150. Kaum einer stellte in diesen tagen die Frage nach Entlohnung voran, sie wollten Arbeitsplätze schaffen, Reparationsleistungen mussten erfüllt werden und Produkte für den friedlichen Aufbau wurden benötigt. Sie waren überzeugt, es geht auch ohne die Rasmusseen, und die Folgen des Krieges sollten sobald als möglich der Vergangenheit angehören.
Das Sprichwort „Not macht erfinderisch“ fand tausendfache Bestätigung, alte Materialien und Teile, die geborgen werden konnten, oft aus Bergen von Trümmern, wurden sorgfältig gereinigt und mit viel Geschick und wenig Werkzeug – an Maschinen war noch gar nicht zu denken – für in dieser Zeit nutzenbringende Geräte eingesetzt. Selbst sowjetische Materialbestände wurden für Reparaturleistungen an landwirtschaftlichen Geräten und alle möglichen Transportgeräte für Güter und Nahrungsmittel eingesetzt.
Auch die anderen Fahrzeugwerke konnten unmittelbar nach Kriegsende an eine Kraftfahrzeugproduktion noch nicht denken. Die Automobilfacharbeiter begannen mit Fahrzeugreparaturen, sie bauten aber auch branchenfremde Erzeugnisse, so z.B.
- in Zwickau: Schrotmühlen, Feuerzeuge, Herde, Sackkarren, Eggen, Kuhketten
- in Zschopau: Ofengestelle, Küchenwaagen
- in Eisenach: Kochtöpfe
- in Suhl: Beile
- in Hainichen: Kartoffelkörbe, Handwagen, Kartoffelquetschen, Kinderroller, Küchenöfen
Es dauerte aber nicht lange, bis die Kraftfahrzeug-Ersatzteilbereitstellung, die Reparatur von U-Motoren und Kraftfahrzeugen verschiedener Fabrikate und der Bau von Gespann- und Handwagen in Hainichen anliefen.
Mit den zunehmenden erfolgen entwickelte sich der gesellschaftliche Aufbau schneller. 1947 zählte die Belegschaft bereits wieder 235 Personen. Einige von damals setzten sich für die Klärung der Eigentumsverhältnisse des Betriebes ein, andere für die operativen Probleme der weiteren Sanierung des Betriebes, sowie für die Schaffung von akzeptablen Arbeits- und Lebensbedingungen.
Es gab keine Anlage, die nicht verschlissen war oder den anstehenden und erst recht nicht den künftigen Anforderungen entsprach.
Über Pläne der Fahrzeugentwicklung wurde viel mit persönlichen Engagement diskutiert und viele Varianten wurden entwickelt. Politische Lehren und Lebenserfahrungen wurden in die Waagschale geworfen, überholte Ansichten mussten überzeugend bereinigt werden und das Wichtigste wurde zuerst angegangen. Die großen Aufgaben dieser Zeit formten Kollektive, festigten Freundschaften, manches gemeinsame Erlebnis entstand.
Der Höhepunkt des schweren Neubeginns war erreicht, als am 17.4.1948 über dem Werktor die Buchstaben VEB – Volkseigener Betrieb – leuchteten. Die Arbeiter hatten sich aus Trümmern einen funktionsfähigen Fahrzeugbetrieb wieder aufgebaut, dessen Eigentümer sie nun auch waren. Als das Werk 1948 zur IFA Vereinigung Volkseigener Fahrzeugwerke kam, zählte es schon wieder 374 Beschäftigte.
Der erste Klein-Lastkraftwagen wurde aus zusammengesetzten Ersatzteilen und Blech-teilen aus noch funktionsfähigen Werkzeugen hergestellt. Er musste aber noch ohne Reifen und Scheibenwischer die Montage verlassen.
Parallel zu diesen das ganze Volk begeisternden Aufgaben wurden Bodenfräsen, vom Typ 20, und Motorhacken, vom Typ 22 hergestellt, die später als Lehrlingsproduktion ein umfangreiches Sortiment Zusatzgeräte erhielten und bei Leistungswettbewerben im Spreewald ebenso bestanden wie zur Landwirtschaftsausstellung in Markkleeberg; 1955 wurde diese Produktion zum VEB Bodenbearbeitungsgeräte Leipzig überführt.
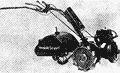
Bodenfräse Typ 20
1949 konnten noch 65 Fahrzeuge V 501 mit selbstgefertigtem
U-Motor ausgeliefert werden. Der wassergekühlte Doppelkolben-Zweitaktmotor mit Gleichstromstromspülung leistete mit 496 cm³ Hubvolumen 17 PS bei 3400 U/min und hatte einen Normverbrauch von 9 l /100 km. Von den 4 Kolben arbeiteten jeweils 2 in einem U-förmigen Verbrennungsraum. Die Pleuel waren auf einem gemeinsamen Hubzapfen der Kurbelwelle gelagert. Mit dem Einsatz von in der DDR entwickelten Zulieferbaugruppen entstand nach dem Anlauf der Typ V 501/2.
wegen der vielseitigen Transportaufgaben in Handel und Gewerbe ist jeder Transporterfertigung die Variante „Fahrgestell mit Fahrerhaus“ die am häufigsten verlangte.
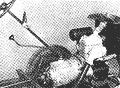
Fahrgestell des V 501
Transportprobleme galt es für viele Wirtschaftszweige zu lösen, und so gab es Abnehmer genug. Folgerichtig verstärkten sich die Forderungen, mehr Fahrzeuge zu produzieren und gleichzeitig technische Weiterentwicklungen zu betreiben. Rationalisierung und Neuerungsvorschläge waren deshalb auch damals schon wesentliche Größen der Entwicklung.
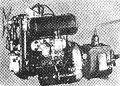
Antriebsbaugruppe des Framo V 901
Mit dem Einsatz des im PKW F9 bewährten Dreizylinder-Zweitaktmotors mit 900 cm³ Hubraum entstand der Framo V 901, mit dem 1951 der Export nach Holland und Belgien wieder aufgenommen werden konnte. 1952 fertigten die 1150 Werktätigen des VEB bereits wieder 1302 Fahrzeuge.
Mit den bisherigen klassischen Transportern Pritschen- und Kastenwagen konnten die wachsenden Bedürfnisse der Abnehmer nicht erfüllt werden, so dass spätere Grundvarianten – Busse, Krankenwagen und Kombiwagen – zu entwickeln waren. Mit leistungsfähigen Karosseriebetrieben wurden die Varianten regelrecht aus dem Boden gestampft.
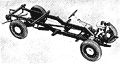
Fahrwerk des V 901
Mit dem Karosseriewerk in Döbeln wurde der erste Kastenwagen vom Typ V 901 und dann die Entwicklungen mit den Kollegen in Halle die langjährigen Serienzulieferungen für die geschlossenen Aufbauten (Holzgerippe mit Blech verkleidet) organisiert.
Hin und wieder waren aber auch noch Aufgaben zu lösen, die – zwar notwendig – die Autobauer nicht sonderlich erfreuten. so wurden die ersten 4 Mähdrescher in der DDR vom Kollektiv in Hainichen nach Unterlagen, die die UdSSR bereitstellte, gefertigt. Die Prototypen vom Typ Stalinez 4 wurden zu Eignungsuntersuchungen für unsere Landwirtschaft eingesetzt und die für unsere Zulieferungen und Herstellungsmöglichkeiten überarbeiteten Konstruktionsunterlagen dem künftigen Mähdrescherwerk übergeben.
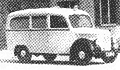
Krankentransportwagen
Immer wieder stand die Frage, wie wird das Werk perspektivisch profiliert, und in diesem Zusammenhang wurden dem Kollektiv weitere zusätzliche Fertigungsaufgaben übertragen, wie der Aufbau einer zentralen Kreisbogenverzahnungskapazität zur Produktion des Differentialgetriebes für den Robur-LKW, die Produktion eines Geländewagens vom Typ H1, wurde später als P2 m im Betriebs-teil Karl-Marx-Stadt (heute Chemnitz) gefertigt, oder die Herstellung eines verschleißfesten Laufwerkes für den Brandenburger Kettentraktor. Die dazu nötige induktive Hochfrequenz-Härteanlage musste selbst gebaut werden.
- Der erste V 901 Komb
- Geländewagen H1
Gewaltige Aufgaben
Im Oktober 1954 erhielt der Autor dieses Beitrages den Auftrag zur Schaffung eines wissenschaftlich begründeten Programms der Transporterentwicklung und zur Organisierung der Produktion. Mit der Kraft aller Kollektive des Betriebes wurden Grundsätze erarbeitet, die erfüllen sollten:
- eine schnelle Weiterentwicklung der laufenden Typen
- die Vorbereitung einer vollkommen neuen Transportergeneration
- die Entwicklung und eigene Herstellung produktiver Fertigungsmethoden und
Fertigungseinrichtungen.
Da der Transporter vom Nutzer als ein Mittel für den rationellen Transport bewertet wird, galt es, mit den Hauptabnehmern eine systematische Analyse, ja sogar eine arbeitsteilige Zusammenarbeit zu organisieren.
Im Ergebnis entstand der V901/2.
Ein verbreitertes Fahrerhaus, ein verlängerter Radstand und eine formschöne Gestaltung waren die äußeren Kriterien des neuen Typs. Aber auch in vielen technischen Details bot der V 901/2 ein fortschrittliche Leistung.
Von vielen Nutzern wurden Spezialaufbauten gefordert: so vom DRK, der Feuerwehr, der Deutschen Post, der VP oder von den Kollektiven des Handels.
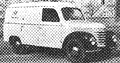
Post-Transporter
Das Herstellerwerk war damit überfordert, denn zugleich wurden ja auch ständig mehr der wenigen Transportmittel benötigt. Für die Spezialfahrzeuge musste also auch eine spezielle Produktion aufgebaut werden. Dies geschah in einigen werken, wie z.B. im Karosseriewerk Halle und im Feuerlöschgerätewerk Görlitz.
Die neue Ära der Transportentwicklung in Hainichen wurde 1957 mit einem neuen Firmenzeichen und der Umbenennung in VEB Barkas-Werke Hainichen eingeleitet.
Seine blitzschnellen und dadurch erfolgreichen Aktionen über das große Reich der Karthager hinweg brachten ihm den Beinamen „Barkas“ – der Blitz – ein.
Und während wieder einmal Soziussättel, Fahrradkippständer, Fußrasten, Fensterbeschläge und Äxte produziert wurden, bereitete sich das Werkskollektiv in aller Stille auf die Produktion einer neuen Transportergeneration vor. Diese sollte den anderen die bewusste Nasenlänge voraus sein. Mit der Formierung des Entwicklungskollektivs, der Erweiterung der Produktionsflächen und Projektierung der Produktionseinrichtungen, der Sicherung der Kapazitäten für Großwerkzeuge, Vorrichtungen, Werkzeuge und Prüfmittel und der vertraglichen Bindung der Zulieferungen standen vor dem Werkskollektiv umfangreiche Aufgaben.
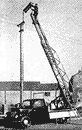
V901/2 als Leiternfahrzeug
Die Erfahrungen der Konstruktion und Technologie wurden diskutiert, es musste in Tag- und Nachtarbeit, im In- und Ausland studiert, verhandelt, konzipiert, projektiert, konstruiert und erprobt werden, um neue Lösungen zu beherrschen.
Ein kleiner Einblick in die Vielzahl der Probleme sei gewährt:
- Wie legen wir Punktschweißverbindungen fest, und wie stellen wir sie her?
- Wie berechnen und erproben wir zeitraffend eine mittragende Karosserie?
- Wie erreichen wir wenig Stillstandszeiten durch Wartungsfreiheit und geringen Verschleiß?
- Wie kommen wir zu einem leistungsfähigen Motor? (Der in Arbeit befindliche fremdgespülte und fremdgeschmierte 1200-cm3-Zweitakt-V-Motor wurde nicht standfest.)
- Kann der Frontantrieb im Transporter akzeptiert werden? (Es gab international noch keinen Transporter mit 1000 kg Nutzlast und Vorderradantrieb.)
- Ist der Einsatz einer vorlaufenden Kurbelachse vorn, also gelenkt, zu vertreten?
- Gelingt eine sphärische Verbundwindschutzscheibe?
- Wie bestimmen wir die Punktschweißzangen?
- Wie bauen wir die Schweißvorrichtungen, besonders die zum Fügen der gesamten Karosse?
- Wie soll das Elektroprojekt ausgelegt werden, damit nicht die Stromstöße aller Schweißvorrichtungen gleichzeitig auf das Netz wirken?
Wie schon geschrieben, dies ist nur ein kleiner Einblick, nur ein winziger Teil von den zu lösenden Fragen.
Die Vorbereitung der Technologie und die eigene Entwicklung der Produktionseinrichtungen waren vollkommenes Neuland, da bis dahin der Holzkarosseriebau, das stabile Fahrgestell mit selbst hergestellten Blechprofilen. die starre Hinterachse und die mit viel Lehrgeld aufgebaute Gleason-Kreisbogenverzahnung für Tellerrad und Ritzel die Technologen und Werkzeugbauer voll in Anspruch genommen hatten.
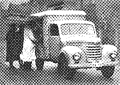
Milchtransporter
Für die grundsätzlichen Festlegungen gab es in der zur Verfügung stehenden Zeit keine Nacheinander-Konstruktions -Technologie. Für komplizierte, aber das Ergebnis maßgeblich bestimmende Entscheidungen wurde gemeinsam mit besonderer Sorgfalt und auch Aufwand für Varianten vorgegangen. So erwies sich z.B. 14 Monate nach Auftragserteilung im Dezember 1955 ein Demonstrationsmodell (Maßstab 1:1) für die Durchstiegs- und Sichtverhältnisse im Fahrerraum als notwendig.
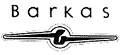
Barkas-Logo
Im Januar 1956 begannen die außer-ordentlich schwierigen und aufwendigen Untersuchungen für die Schweiß- und Montageanlagen und die ständigen Rückkopplungen zu den konstruktiven Details.
Die gesamte Prozessplanung konnte anhand ausgearbeiteter Varianten nach 23 Monaten entschieden werden. Einen Monat später, genau nach 2 Jahren, erfolgte der Abschluss der Konstruktion der Karosse, womit der Startschuss für die Anfertigung der Groß-Werkzeuge gegeben werden konnte.
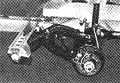
B-1000 Transporter
Vollkommen neue Lösungen, besonders des Fahrwerkes, mussten zusätzlich zur Berechnung vor der endgültigen Einordnung in das Gesamtprojekt versuchstechnisch erprobt und in zeitraffender Prüfung bestätigt werden. Unter Nutzung exakter Vergleiche mit Fahrzeugen anderer Fabrikate galt es, das Risiko einzugrenzen. Auch hier nur wieder einige Beispiele: Die Wirkung der Handbremse auf die Vorderräder ergab sich aus der Tatsache, dass bei der gewollten Achslastverteilung die Handbremse an den Hinterrädern entweder ein Blockieren auslöst bei gesetzlich festgelegter Mindestverzögerung des leeren Fahrzeuges oder dass das voll beladene Fahrzeug nicht genügend verzögert werden kann. Überbremste Vorderachsen führten aber zum Abheben des hinten unbelasteten Fahrzeuges.
Hartnäckige Gegner des Frontantriebs, die schlechte Erfahrungen mit frontgetriebenen PKW gesammelt hatten, erzwangen eine Demonstration mit Fahrversuchen, in denen am Goßberger Berg bei verschiedenen Straßen- und Beladungszuständen und präparierten Vergleichsfahrzeugen die Theorien der jungen Ingenieure bewiesen wurden und neue Mitstreiter gewonnen waren. Natürlich musste mit gleicher Energie für den großvolumigen „schlauchlosen“ Reifen 6.70—13 „Extra Transport“ gestritten und eingetreten werden, sonst hätte der B 1000 nicht seine sprichwörtliche Bodenhaftung, als Optimum von Reifenauflagefläche, Achslast, Federung und Dämpfung. Die vorn vorlaufende Kurbelachse und hinten nachlaufende Kurbelachse sind mit den Drehstäben, die für alle vier Räder gleich wartungsfrei gelagert sind, so angeordnet, dass alle vier Drehstabfedern in einem Winkel von 700 spiegelbildlich symmetrisch zur Fahrzeuglängsachse arbeiten. Bei langen Federwegen hat diese patentierte Anordnung eine vorteilhafte Beeinflussung von Nick- und Kurvenneigung ermöglicht.
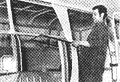
Karosseriebauer
Vom Transporter werden hohe Anfahr- und Steigleistungen verlangt, ebenso Fahrgeschwindigkeiten ähnlich den PKW’s, also musste die Drehmomentkurve des Transporters anders sein als beim gleichen Motor im PKW Wartburg — auch ein neues Getriebe musste her. In der schnell erweiterten Versuchsabteilung wurden die Holz-Klopf-Modelle im Maßstab 1:1 und die Funktionsmuster zur Erprobung gebaut.
Die hohe Qualität des Musterbaues und die rund um die Uhr durchgeführte harte Rundstreckenerprobung, nicht immer zur Freude der Bewohner in den Dörfern um Hainichen, weil Straßen dort noch schlecht genug waren, bestätigten die progressive Konzeption und damit auch die Aussage: Bei niedrigen Kosten ist bei einem Eigengewicht von 1,1 t eine Nutzlast von 1 t zulässig. Bis zum Anlauf der Nullserie wurden 1.052.600 Erprobungskilometer gemeistert.
Nun konnte mit aller Kraft die endgültige Technologie festgelegt und anhand detaillierter Terminpläne der Vorbereitungsprozess geleitet und kontrolliert werden. Nach all den Mühen um das neue Fahrzeug freute sich das gesamte Betriebskollektiv, als 1958 unser neuentstandenes Fahrzeug von Partei und Regierung der DDR Lob und Anerkennung erfuhr. Mit Wirkung vom 1. 1. 1958 wurde dann auch folgerichtig der VEB Barkas-Werke Karl-Marx-Stadt gegründet. Mit ihm wurden 5200 Beschäftigte aus den Betrieben Barkas-Werke Hainichen, Motorenwerk Karl-Marx-Stadt und Fahrzeugwerk Karl-Marx-Stadt vereinigt.
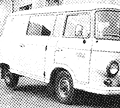
B-1000 Transporter
Doch der Anlauf der Serienproduktion des neuen Typs verlangte dem Betriebskollektiv alles ab.
Selbst die Kollektive, die in dieser Zeit den Motor für den PKW Trabant zum Anlauf bringen mussten, ebenfalls mit selbstgebauten neuen Einrichtungen, halfen mit am Aufbau der Transporterproduktion.
Das Fahrzeugwerk wurde vollständig um-gebaut, hauptsächlich für die Produktion der Transporterkarosse und für die Montage und das Prüffeld des luftgekühlten Zweizylinder-Zweitaktmotors für den Kleinwagen Trabant. Etwa alle 2 Jahre musste die Stückzahl des Trabant-Motors verdoppelt werden. Die Leistung des Motors war stetig zu steigern und der Kraftstoffverbrauch zu reduzieren. Auch die Weiterentwicklung des Trabant-Motors, z.B. von 500 auf 600 cm³ kostete viel Kraft.
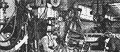
Fertigungsstrasse
Der selbsttragende Wagenkörper für den B 1000 in Ganzstahlausführung nach der Schalenbauweise forderte vollkommen neue Technologien und Fertigungseinrichtungen. Eine Halle im Betriebsteil Karl-Marx-Stadt wurde praktisch umgepflügt, um die sehr umfangreichen Ver- und Entsorgungseinrichtungen für die Schweißeinrichtungen und rund 1200 Luftspannelemente (Luft, Wasser, Strom) zu verlegen. Neben der hauptsächlichen Widerstandspunktschweißung kam nur in Einzelfällen Autogen- und Elektrodenhand-schweißen zum Einsatz.
Zur Rohkarossenfertigungsstraße wurden von beiden Seiten die in der gleichen Halle gefertigten Baugruppen zugeführt. Alle Großvorrichtungen für das Fügen der Blechteile, Baugruppen und die vollständige Karosse wurden im Werk von ausgezeichneten Betriebsmittelkonstrukteuren entwickelt und im eigenen Rationalisierungsmittelbau unter Berücksichtigung vieler Neuerungen der Arbeiter gebaut.
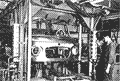
Hauptschweißstrasse
Nicht schlechthin die Begeisterung für den Transporter, sondern auch das Wachstum der Volkswirtschaft führte zur sprunghaften Zunahme der Kraftfahrzeugbestände. Die Marktanalyse stellte besonders progressive Forderungen für die Verteileraufgaben des Handels und im Dienstleistungsbereich, also eine Herausforderung für die Fahrzeugkategorie Transporter.
Die Forderungen an den Transporter wurden immer deutlicher:
- qualifizierte Beförderung von Personen und Transport von Waren
- großes Ladevolumen bei geringer Verkehrsfläche (Nutzmasse ist mitunter zweitranig)
- günstige Ein- und Ausstiegsmöglichkeiten nicht nur für die Fahrgäste, sowie vorteilhafte Be- und Entladung (niedrige Ladehöhe)
- niedrige Anschaffungs- und Betriebs-kosten bei großer Transportleistung
- zugelassen für PKW-Fahrerlaubnis (bis 8 Personen bzw. 2,5 t Gesamtmasse)
- leichte Bedienbarkeit mit PKW-ähnlichen Handhabungskomfort
- Grund- und Sonderausführungen mit möglichst großem Rationalisierungseffekt beim Nutzer
- hoher Standardisierungsgrad mit anderen Fahrzeugen und Zulieferteilen
- gute Manövrierfähigkeit
Forderungen, die allein mit den Grundausführungen des 1. Produktionsjahres nicht zu erfüllen waren.
Wieder einmal waren viele Spezialfahrzeuge gefragt.
Im 3. Jahr der Serienproduktion – also 1964 – standen insgesamt 16 Varianten zur Verfügung, einige davon zeigen diese Bilder:
- B1000
- Bereitschaftswag.
- Kleinlöschfahrz.
- Drehleiterfahrz.
Die Unterstützung, die das Werk vielen Expeditionen und Betrieben für Auslandseinsätze gab, war kluge Werbung mit besonderer Schwachstellenforschung unter extremen Bedingungen, so auch die Ergebnisse der Orient-Expedition 1965/66, beschrieben in den Büchern „Pässe – Pipelines – Pyramiden“ und „Wüsten – Wadis – Wasser-Räder“.
„Als die Passhöhe geschafft ist, klopfen wir wieder einmal unserem Barkas anerkennend aufs Armaturenbrett. Wir mussten unsere „Mähre“ nicht tragen oder schieben! Auf den letzten fünftausend Kilometern wird uns unsere Barkas wohl kaum noch im Stich lassen. Er hat es während der ganzen Reise nie getan! Er ist nach wie vor der geachtete Vierte unseres Expeditionskollektivs. Ein Spitzname hat sich für ihn immer noch nicht gefunden, und das spricht für ihn! Der Vorschlag „Schaukelpferd“, der auf den welligen Wüstenpisten Libyens und Jordaniens ins Gespräch kam, war auf halbwegs normalen Straßen sofort wieder vergessen…“
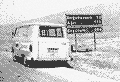
Barkas-Bus
Von uns Vieren hat der Barkas – das gestehen wir restlichen drei neidlos ein – zweifellos am meisten leisten müssen: 2000 Meter Steigung in knapp 2 Stunden, regennasse, glitschige und heiße, klebrige Asphaltstraßen, stoßdämpferfressende Waschbrettpisten, steinige Flussdurchfahrten, tückische Sandverwehungen. Er hat weder bei Schneesturm und sechs Grad minus noch bei Sandsturm und 48° C im Schatten gestreikt. Er brachte uns auf 2000 Meter Höhe und hinab 400 Meter unter NN. Er wurde nie schwach. Auf schwierigen, kurvenreichen und oft sehr langen Steigungen hatte sein Motor stets so viel Reserven, dass er selbst die „härtesten Knochen“ schaffte. Steigungen bis zu 25 % wurden noch im 2. Gang bewältigt…
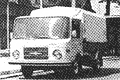
B 1000
Trotz aller Anstrengungen, die wir ihm zumuten mussten, war er nicht einmal besonders „gefräßig“. Wir verbrauchten im Durchschnitt nur 10,7 l auf 100 Kilometern! Das sind Lobgesänge. Was aber waren die Schwächen? Nun ja, in der dünnen Luft von 2000 Metern muckerte er manchmal und wollte nicht sofort anspringen. Aber dort oben viel auch uns das Atmen schwer. Und bei mörderisch langen Abfahrten qualmten einige Male die Bremsen. Wir haben es ihm nicht übelgenommen! Wer würde, sagten wir uns, nicht ins Schwitzen kommen, wenn er auf so steilen Straßen eine solche Tonnenlast und 5 Zentner Übergewicht halten müsste.
Im Reigen der Automarken aus aller Welt konnten wir uns mit unserem rollenden Haus sehen lassen! Auf den Campingplätzen war unser Erscheinen stets eine Sensation. Da der Barkas nicht sehr bekannt war, wurde er von den motorisierten Globetrottern sofort auf Herz und Nieren geprüft. Und er schnitt dabei nie schlecht ab. Bei diesen Besichtigungen faszinierte, von unser „komfortablen“ Eigenbau-Innenausstattung einmal abgesehen, vor allem die Größe des Innenraumes, die Breite, eine gute Sicht nach allen Seiten ermöglichende Fensterfront und das bequeme Sitzen hinter dem Steuer…Wären wir Kaufleute, wir hätten mit dicken ausgefüllten Auftragsbüchern heimkehren können…“
Kaum einer anderen Fahrzeugkategorie sind so viele Möglichkeiten der friedlichen völkerverbindenden Mission gegeben. Viele Vorhaben in Ländern, die gern die Hilfe der DDR in Anspruch nehmen für die soziale und industrielle Erschließung ihres Landes, wurden meist durch die vorteilhaften Service-Möglichkeiten erst wirksam.
Entsprechend dem sich bewährenden Konzentrationsprozess in der Industrie wurde ab 1.1 1979 eine neues Kombinat gebildet, in dem die Barkas-Werke jetzt auch als Stammbetrieb fungieren.
Dem IFA-Kombinat für Personenkraftwagen, Pkw-Motoren, Stationäre Motoren, Diesel-Einspritzungen, Wohnwagen, Wohnzelt-Anhängern, Stoßdämpfern, Kupplungen, Kühlern, Gelenkwellen, Scheibenrädern, Kugellenkkränzen, Lenkungen, Heizungen, Abgasanlagen, Fahrzeugfedern, Schlössern, Einspritzungen, Einspritzdüsen und Einspritz-Elementen an.
Wie die Typenübersicht 1961 bis 1985 zeigt, wurde der Transporter ständig weiterentwickelt und in seinem Gebrauchswert gesteigert.
Framo aktuell: Elektromobilität
Eine Neugründung unter dem Namen Framo erfolgte 2014 durch Andy Illgen. Das im sächsischen Langenbernsdorf ansässige Unternehmen hat sich auf Elektromobilität spezialisiert und bedient insbesondere die Logistikbranche. Framo nimmt beispielsweise die Elektrifizierung von Lastkraftwagen vor, wobei nahezu sämtliche Aufbauten bedient werden. Die Simulation eines Verbrennungsmotors erfolgt durch ein innovatives Steuergerät namens CuroControlSRx.
Die Geschichte der Fahrzeugherstellung der Framo- und Barkas-Werke sowie ihrer Modelle findet sich lückenlos aufgearbeitet im Erlebnismuseum für Stadt- und Industriegeschichte Frankenberg/Sa.
Das seit 1996 existierende Museum fokussiert sich insbesondere auf die Geschichte der Nutzfahrzeuge. Die verschiedenen Modelltypen der Marken Framo und Barkas werden hier mit derzeit 19 restaurierten und aufbereiteten Originalen ausgestellt. Insgesamt bietet das Museum über 100 Exponate, wobei auch Einblick in die Technik gewährt wird. Zu diesem Zweck finden sich geöffnete Fahrzeuge, Fahrzeugteile und Schnittmodelle, die es ermöglichen, die Funktionsweise nachzuvollziehen.
Die heutige Verfügbarkeit von Ersatzteilen ist eigentlich recht gut, es gibt inzwischen ein Vielzahl von Neuanfertigungen. Basisersatzteile wie bspw. Zündkerzen oder Ähnliches kann man auch hier finden.
Die Geschichte von Framo und Barkas wird von vielen privaten Fahrzeugliebhabern am Leben gehalten, so finden etwa in Döbeln, Frankenberg und anderen sächsischen Städten über’s Jahr verteilt, Treffen statt.